Canadian film and TV design pro creates face shield for health-care workers
John Allen has worked on Suicide Squad, Star Trek and Total Recall. Now he's designed a COVID-19 shield
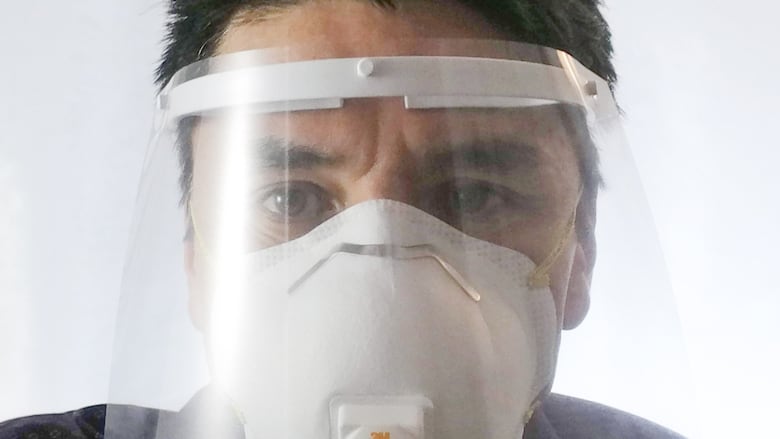
Artists around the world have been helping people through the COVID-19 crisis by offering things like online concerts, free classes, and storytelling for kids.
But John Allen has put his skills to work in an entirely different way: by designing mass-producible face shields for frontline health-care workers.
Allen is normally a prop designer for film and TV who was worked on Suicide Squad, Star Trek and Total Recall, to name a few.
Then recently, a friend who works at a medical clinic texted Allen an image of a 3D printed mask, and asked the concept design and 3D CAD modelling expert if he could print some. He answered that he could — but knew he could do even better.
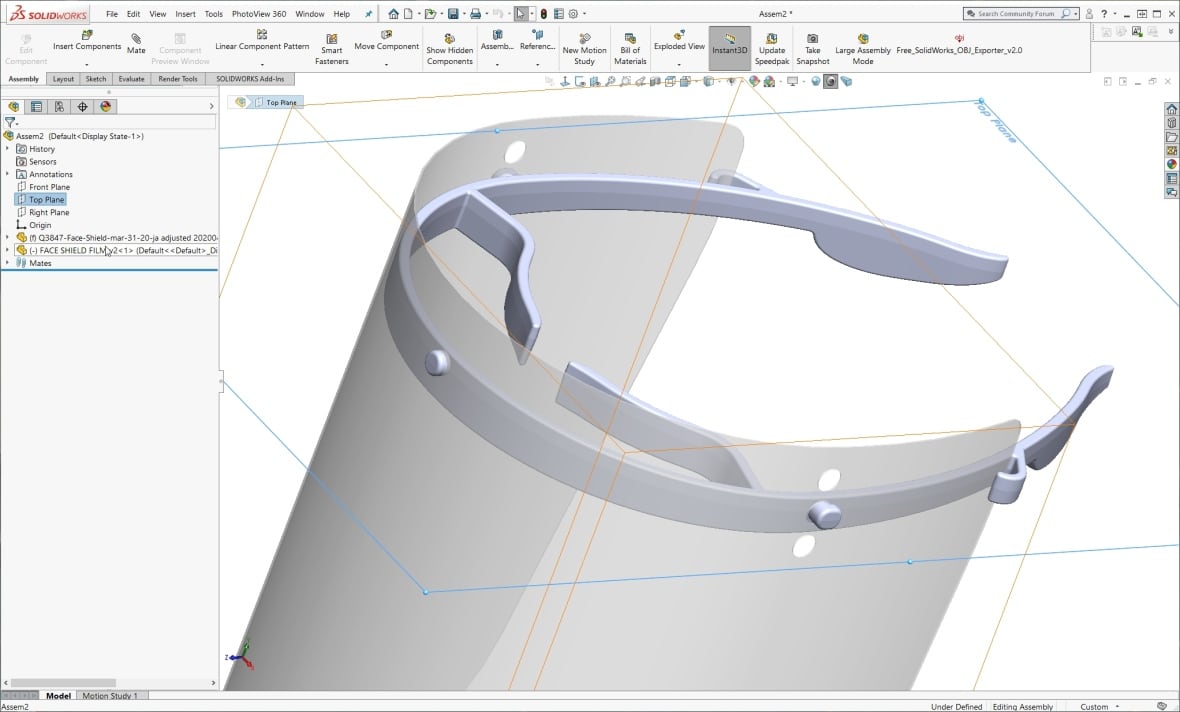
'There has to be a faster way'
"We have a whole bunch of 3D printing heroes out there trying to answer this cause," says Allen in an interview with q host Tom Power. "And I use 3D printing all the time for my work, but it takes an hour or two to print most things. And I just thought, 'There has to be a faster way.'"
So Allen contacted his film and TV design colleague Peter Colpitts.
"I said to him, 'Look, they're asking people to 3D print all this stuff. Don't you think we should just make a mould, and injection mould these?'" remembers Allen, who is based in Goodwood, Ontario.
"And he was totally onboard. Right off the bat, we were thinking exactly the same thing."
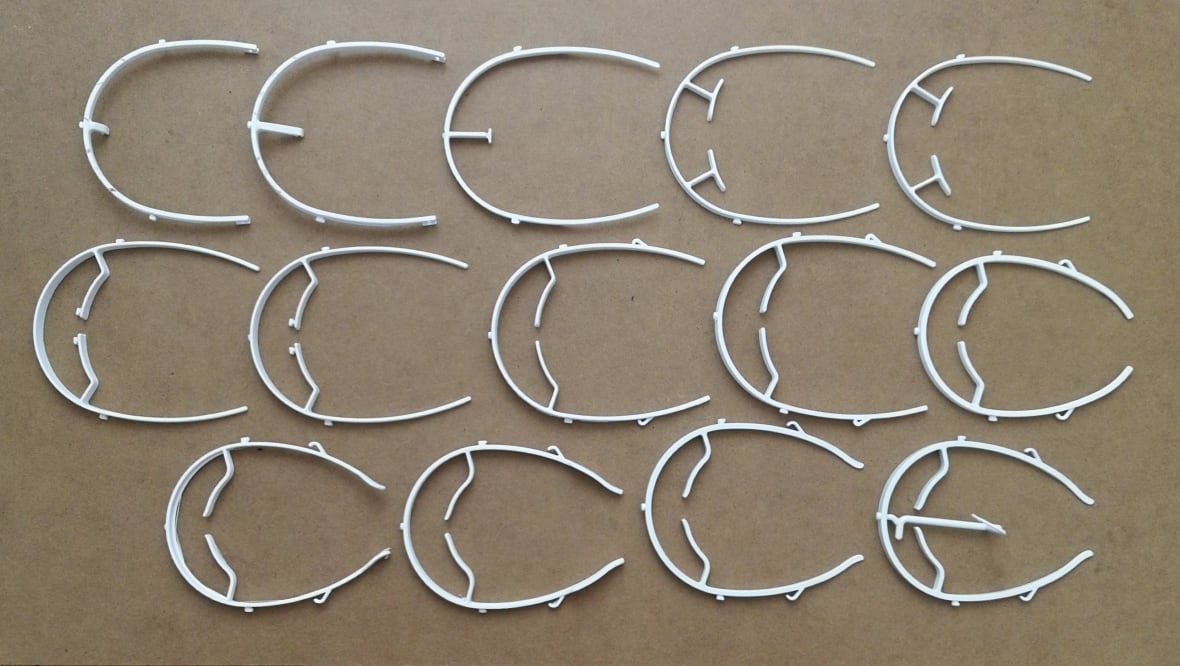
Together, Allen and Colpitts designed a shield that consists of two parts: a plastic piece that goes across the face, and a moulded frame.
"It's injection moulded out of ABS so it's strong. And we believe it's recyclable. It's reusable as well," says Allen. "We believe it can be cleaned and sterilized and used again effectively."
'I became obsessed'
They can also be made quickly. A typical 3D printer can create one shield per hour; a medium-sized mould station, however, can produce four shields per minute — roughly 240 times more. Already a manufacturer has stepped up, and said they can produce 15,000-20,000 of the masks per week.
The shields are an essential component of personal protective equipment, or PPE, that hospital workers use when working around people infected with COVID-19.
Allen hopes they will be useful primarily for frontline health-care workers, but adds that they could also be used for other types of workers who need additional protection, such as grocery store stockers.
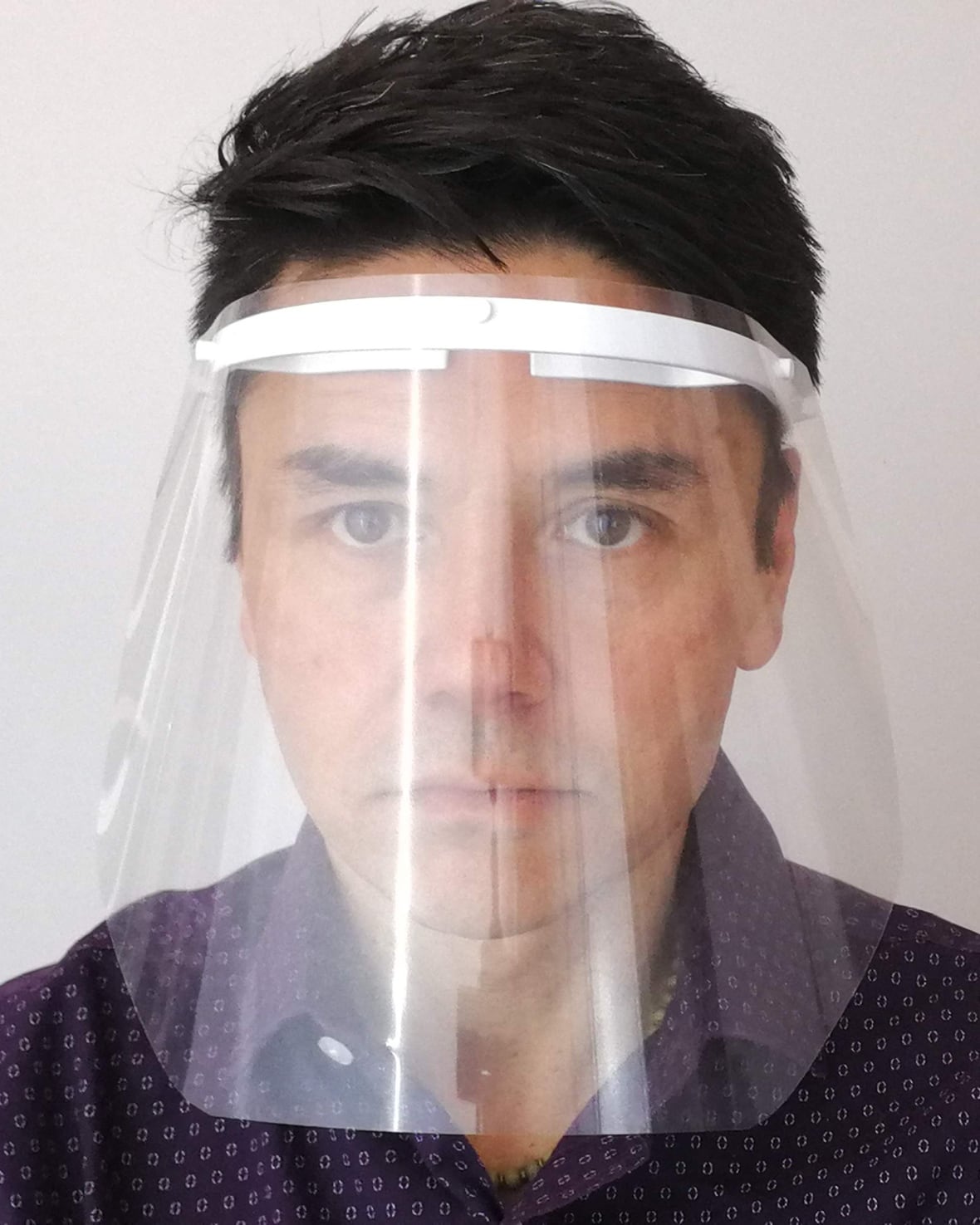
Like many people, Allen enjoyed his first week off work, and thought he'd be able to finally finish his bathroom reno, or maybe have time to make art — but his new passion has taken over.
"I wanted to draw. I wanted to paint. I wanted to do all these things. And then oddly enough, with this coming up, it just kind of refocused my mind. Ask my wife," says Allen with a laugh.
"I became obsessed with the idea of doing something that I thought could help out."