Scientists have found a way to harden wood to make a knife that rivals steel
Process uses chemistry and pressure to make ordinary wood 23 times harder
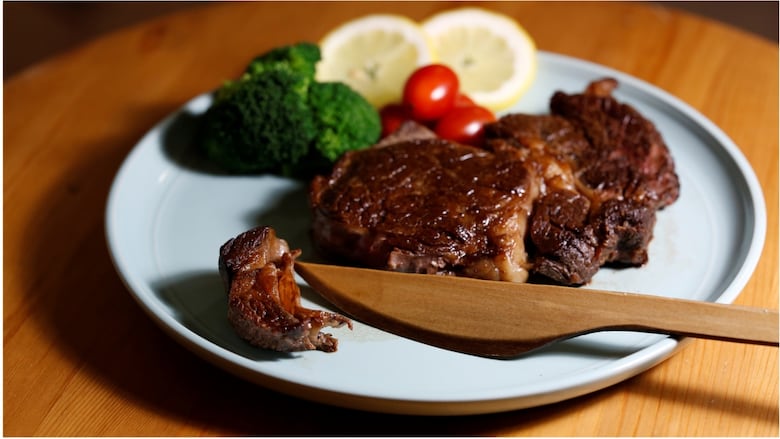
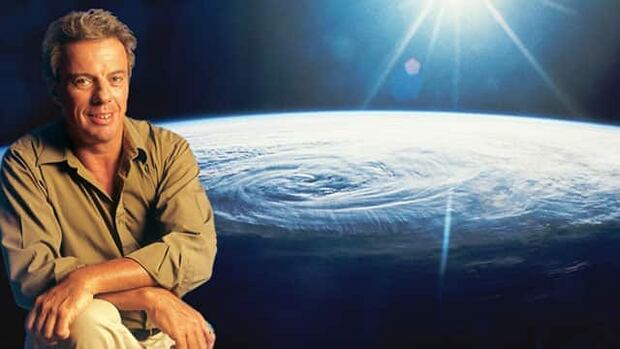
Scientists have developed a process that allows them to manipulate wood to make it denser and harder than the natural product. They used the resulting material to make items like wooden knives and nails that rival traditional steel.
Teng Li, a materials scientist and mechanical engineer from the University of Maryland, told Quirks & Quarks host Bob McDonald that he and his colleagues made the wooden knife to demonstrate the new process they developed.
"Surprisingly, our wooden knife is actually three times sharper than the typical stainless steel dinner table knife," he said. "It can achieve its purpose of cutting medium well-done steak very nicely without breaking."
Their findings were published this month in the journal Matter.
Li added that the knife can be sharpened when it becomes dull, and even survive the dishwasher.
Improving natural wood
The process of making hardened wood is really quite simple, said Li. Wood gets much of its strength from cellulose, the substance that makes up the fibres of the wood.
Cellulose itself is a remarkably strong material, whose strength relative to its density is "higher than almost all the metals and alloys in the world," said Li.
But cellulose comprises only 40 to 50 per cent of wood. So the first step in developing a higher-density wood-based material was to reduce the components that weren't cellulose. In particular they targeted lignin, which acts like a kind of glue in normal wood, binding fibres together.
"We use chemicals to partially remove lignin. And after the first step the wood becomes soft, flexible and somewhat squishy," said Li.
"So the second step is that we apply pressure. We also increase the temperature. The purpose of that is to really densify the natural wood and also remove the water, reducing its thickness to around 20 per cent of the original natural wood."
WATCH l This higher-density wood has many applications, including at the dinner table.
The result is an incredibly strong material, comprised mostly of cellulose, that is 23 times harder than it was to start.
Microscopic analysis of the finished wood product revealed that the process had significantly reduced natural defects in the wood, collapsing space between the fibres, and even pores and tiny pits in the cell walls of the wood. The compressed material showed very little tendency to bounce back to its original thickness.
Wooden nails and truly hard hardwood floors
The success of Li's process suggests there are also applications beyond the dinner table.
"We also demonstrated that you can use these hardwoods to make nails as functional as steel nails," said Li. "We know steel nails rust over time. But the wooden nail won't suffer from this problem. And in our daily life, you see many hard materials, for example flooring. You can have this hardened wood over a large area that can be coated to reduce scratching."
WATCH l A wooden nail is hammered through three boards.
Renewable and sustainable
There is also the possibility that wood processed in this way could replace existing products that are known to be harmful to the environment, said Li.
"I think there is huge potential to have these wooden utensils help mitigate the environmental concerns raised by the use of the plastic utensils. We developed a straw made of cellulose, which is biodegradable and with a comparable performance to plastic straws."
Li suggests that because natural wood includes the same components, cellulose and lignin, this process could be applied to wood from any species of tree.
"Trees are renewable and wood is sustainable," he said. "If we look back to mother nature, we can use this natural material toward a sustainable future."
Written and produced by Mark Crawley