London researchers revamping jawbone surgery with 3D printing technology
Experts at ADEISS are working with surgeons to help streamline bone operations
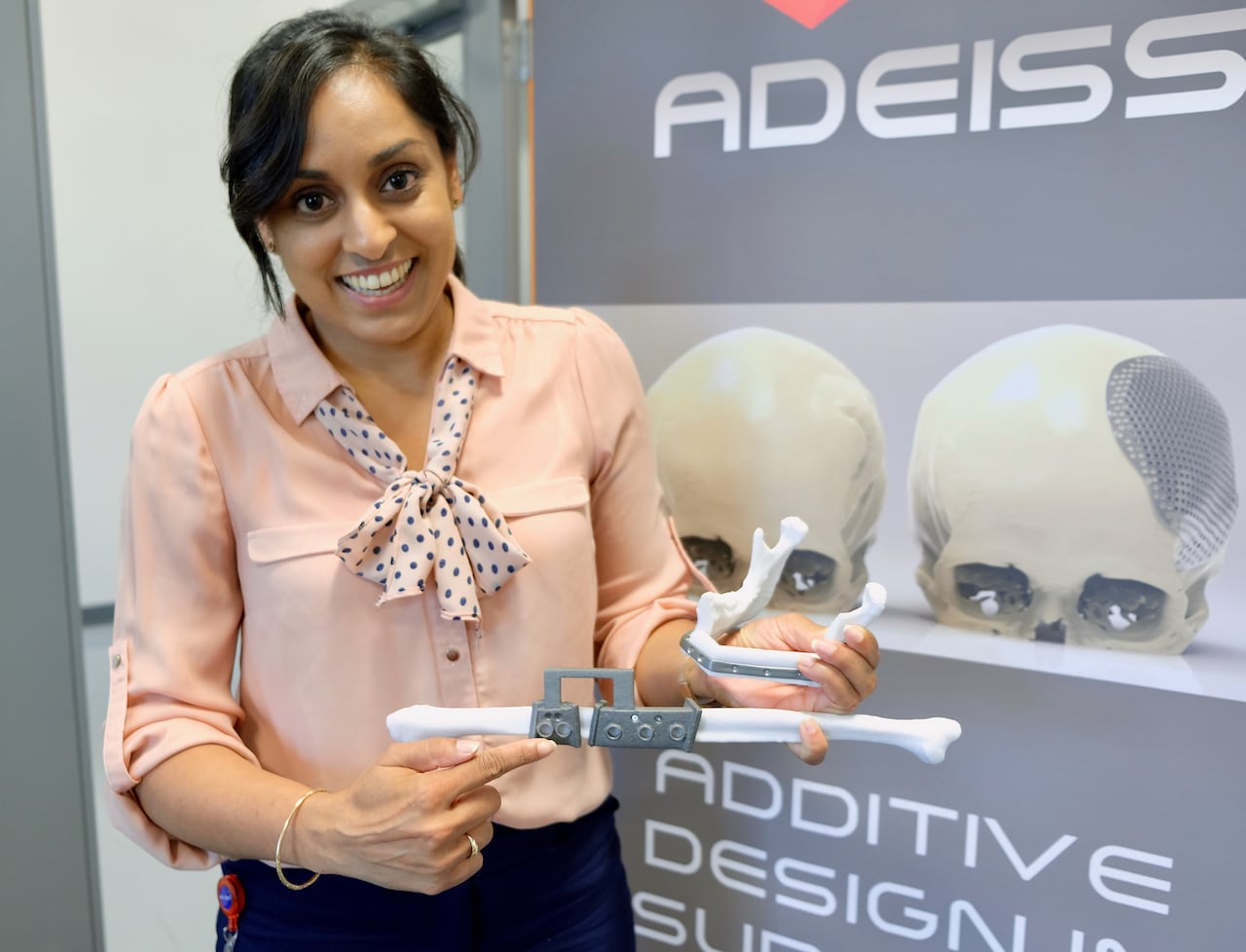
London researchers are revamping jawbone surgery with 3D-printing technology
New 3D-printed surgical guides and jaw implants could soon help patients in need of reconstruction surgery. And they're printed right here in London.
"If you think back ten or twenty years ago, a surgeon would plan a procedure like this almost entirely from X-Ray projection images," said Dr. David Holdsworth. He's the scientific director at ADEISS, a local 3D-printing incubator and manufacturer of metal surgical devices.
"But now we're in an era where you could produce a physical 3D model that a surgeon could hold in their hands before the surgery."
The prototypes are notable because they're individually crafted to fit each patient's unique skeleton.
The guides show surgeons exactly where to cut and screw, while the implants are designed to replicate the original bone structure as closely as possible.
"The hope is that it will cut time in surgery. Time in surgery is money, so it helps to make the surgery more cost effective," Holdsworth said. "But it's also good for patients, cause you want to spend as short a time in the operating room as you can."
And after months of development, ADEISS will finally be showcasing their new technologies at Western University in September. Health Canada will take a look in the fall, at which point the products could finally get approval for human use.
In the meantime, ADEISS has been making inroads into veterinary surgery. Mostly they've made skull plates, a number of which have been successfully implanted in dogs.
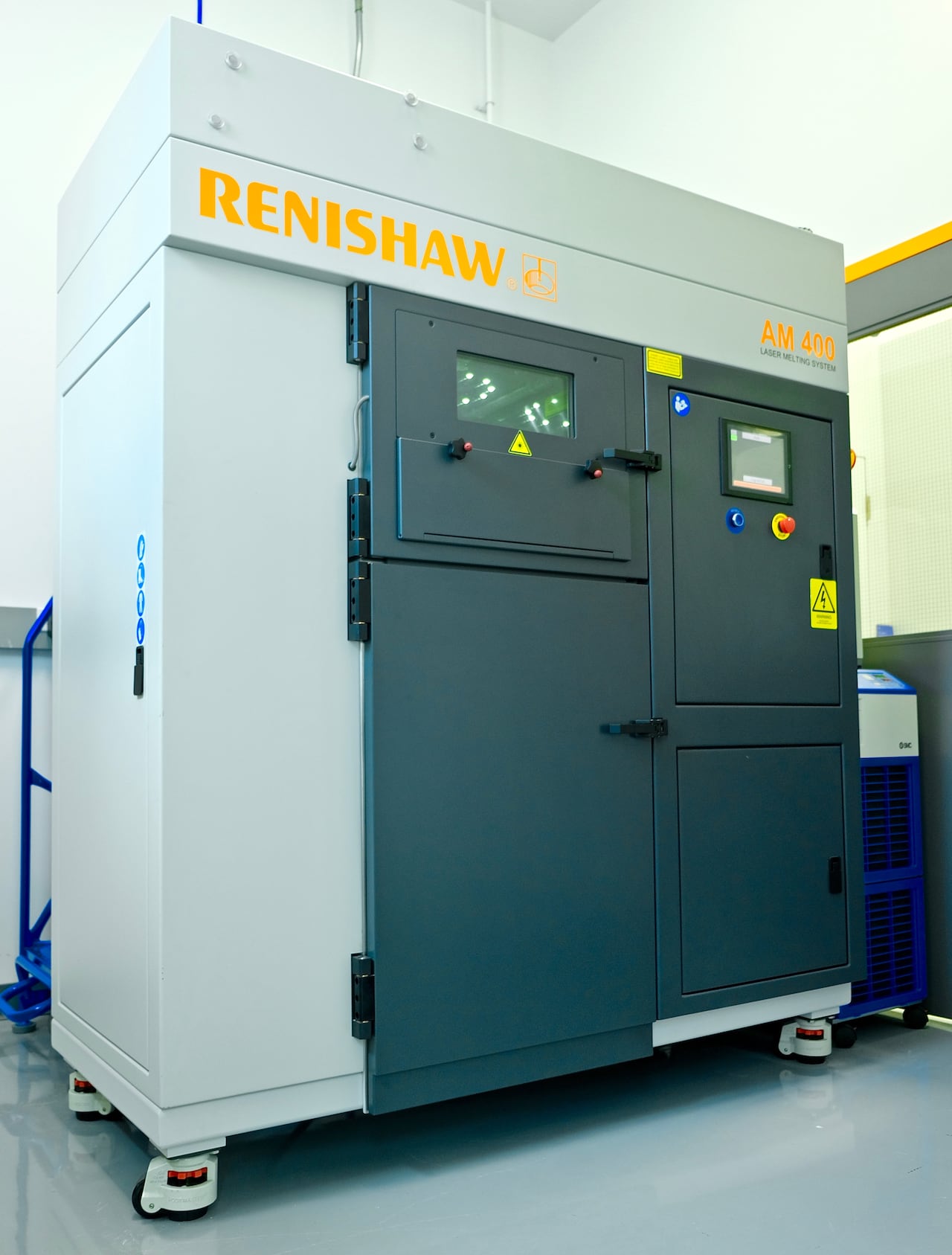
Optimising orthopaedics
ADEISS developed the jawbone products with the help of local maxillofacial surgeons.
One of the surgeries they've been working to streamline is fibular flap surgery, a common method of jaw reconstruction surgery
"That's an ideal application for a customised approach, of course, because everybody's jaw is slightly different," Holdsworth said.
The procedure is used when cancer or severe trauma damages the jaw beyond repair. Surgeons will actually remove your fibula and use it to rebuild sections of jaw.
"They do this by doing specific cuts to reform that natural structure of the bone," says Dr. Yara Hosein, the applications specialist at ADEISS. "With surgical guides, that we can work again with the clinician to develop, we can technically create guides that the surgeon wants."
Surgeons have traditionally relied solely on imaging X-Rays and, more recently, CT scans to plan their surgeries.
But with 3D printed models surgeons hold plastic replicas of patients' bones in their hands.
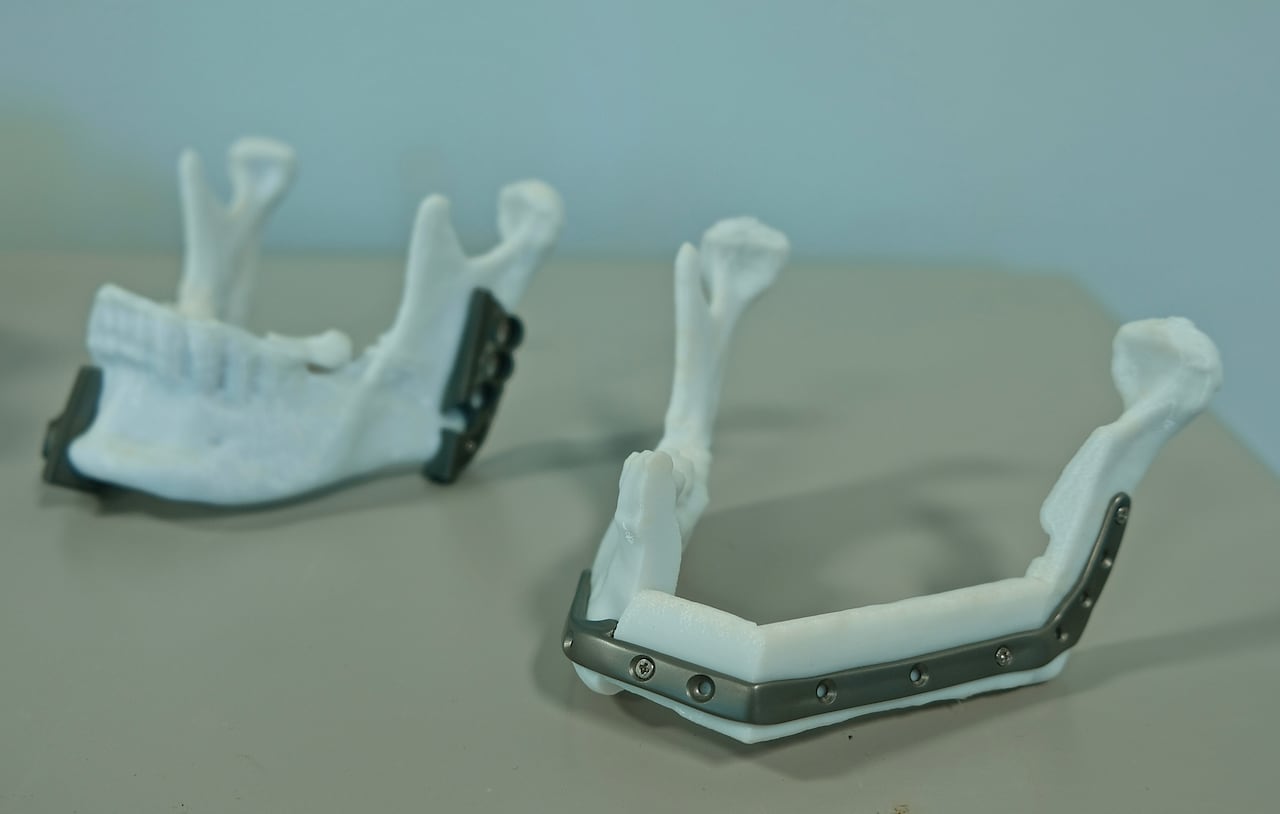
And with ADEISS' metallic guides, surgeons can design their tools to know precisely where to cut and screw into the fibula and jawbone. "Now they have an actual step-by-step process, you cut here, these are your screw-in holes," Hosein said.
Current surgical methods require physicians to tediously bend metal components into a similar shape as a patient's' jaw.
But with 3D printing, manufacturers can print bone supports or identical implants or restore patients' jaws as accurately as possible.
"So no longer is the surgeon required to sit there and bend to match the anatomy of the patient, you can now print the exact match of that plate and provide that with the surgical guide," Hosein explained.
That's why ADEISS manufactures their products on a case-by-case basis making precise tools for a specific patient.
They first start with a 3D model of a patient's skeleton generated by CT scans. Complex printing software then generates schematics based on the shape of their bones.
Next flour-like titanium is fed into the massive printer and a 400-Watt laser molds the powder into layers 50 microns tall. That's about half the thickness of a sheet of paper.
And layer-by-layer, it constructs the devices.
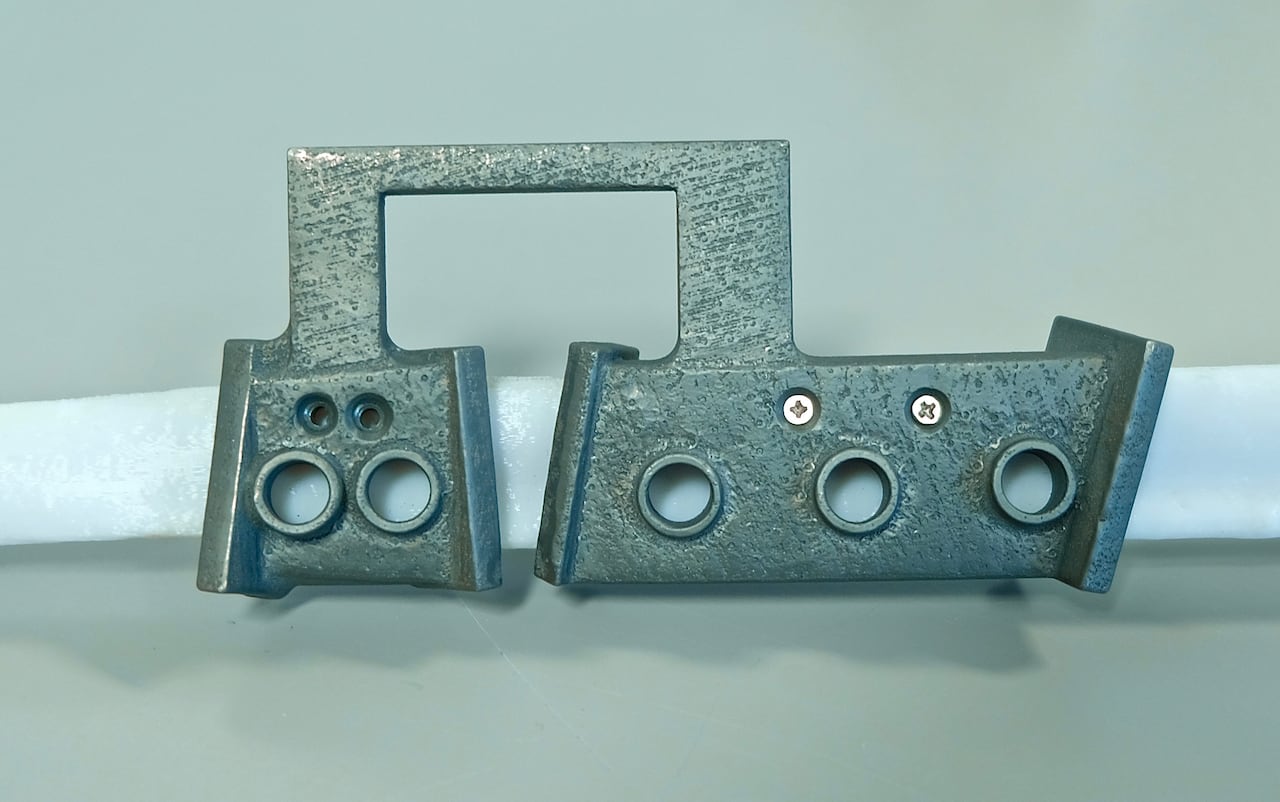
Safer implants
Unlike older methods of manufacturing, 3D printing allows an unparalleled level of detail and intricacy.
They can create porous latticeworks throughout the entire implant, for instance.
"Traditionally you'd place an implant and actually cement it in place, the idea with having a lattice is that you could put it in place, you could introduce material to encourage bone to actually grow into the lattice," Parkes explained.
This would give the bone a firmer grip on the implant, reducing the chance of it loosening over time. And it can also make them more flexible and behave more like natural bone.
"If you imagine a traditional metal implant it'll be solid material, and that's a lot stiffer than natural bone," Parkes said.
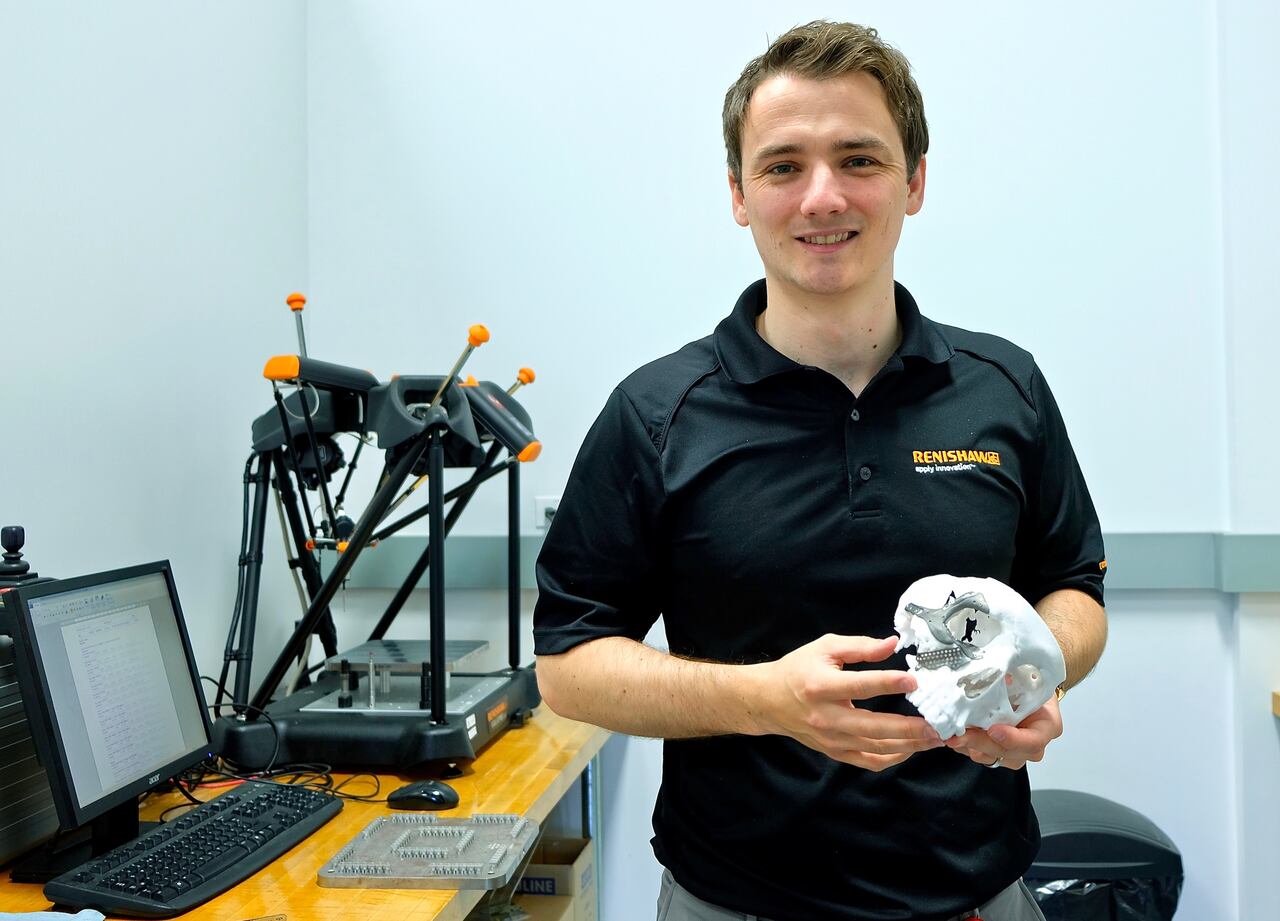
That can lead to an effect called stress-shielding, where tissue recedes from the implant, something surgeons hope to avoid.
But for now human patients will still have to wait for these products to hit the market.
"In 2019 we expect we'll be testing several new components in patient trials here in London," Holdsworth said. "So the next year is going to be very exciting for the team."
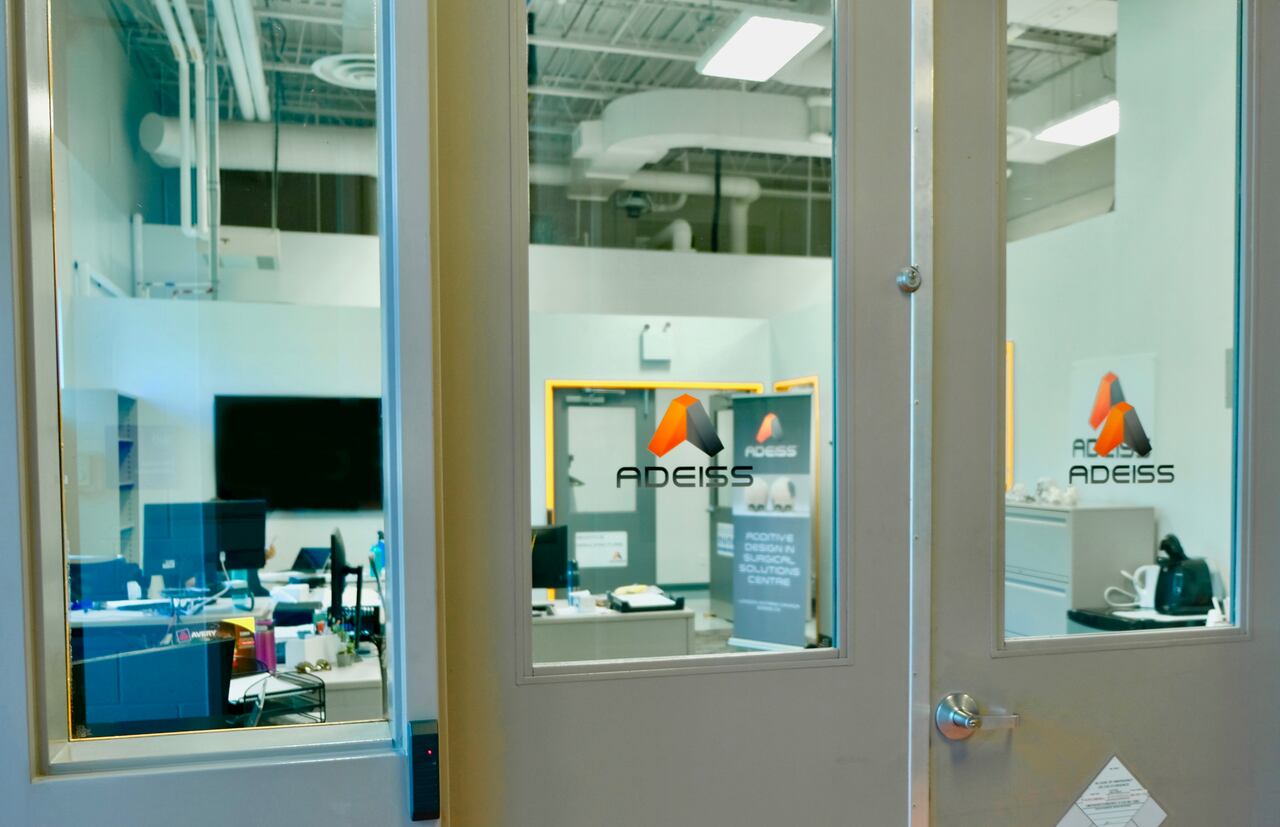