Is the future of mining electric? As mines transition equipment, new risks emerge
Mining industry has long been powered by diesel, but that’s changing
Canadian mining companies are starting to cast aside the diesel-powered trucks, loaders, and drills that have long-been the backbone of the industry for electric alternatives — a move that some industry experts say could make mining safer and less polluting.
Mario Santos, mining director for Unifor, Canada's largest private sector trade union representing 9,900 mining and smelting workers, said he welcomes the shift. "I think it's a positive change. It's better than the processes we were using before," he told CBC News.
Management consulting firm McKinsey & Company estimates that the mining industry accounts for four-to-seven per cent of global greenhouse gas emissions, and industry members say electric mining equipment has the potential to lower these emissions while also reducing operating costs.
More importantly for workers who spend their days operating heavy-duty machinery deep beneath the earth's surface, this switch would clean up the diesel-filled air they breathe day-in and day-out.
But — as the union leader is quick to point out — this change also presents new operational challenges and safety risks. And although electric equipment has been slowly trickling into mines for over a decade, some say there's still work to be done to bring safety standards and training up to speed.
"Until we move to a point where we're able to eliminate those risks — which is a tough thing to do — there's always going to be a concern," Santos said.

'Electrification is the only solution'
Today, many important mining tasks can be accomplished with electric equipment. Electric drills are used to dig into rock, electric vehicles — like trucks and loaders — help move material around sites, and electric conveyor belts and pulley systems do the same.
North American mines started testing out heavy-duty electric equipment — mainly vehicles attached to electric trolley lines — in the 1990s. But, Canada was one of the first countries to introduce battery-powered electric vehicles to mining in 2012.
Most in the industry were hesitant to be the earliest adopters of the new and largely unproven technology, said Dale Rakochy with Sandvik Mining and Rock Solutions, a Swedish engineering company that produces electric and diesel-powered mining equipment.
"Nobody wants to really be the Guinea pigs with new technology because it does pose some challenges for operations," he said.
WATCH | Electric zambonis prevent toxic fumes:
Now, after nearly a decade of use, the technology is proving its worth and hesitancy is dissipating, said Rakochy. He's seeing more mines interested in going electric.
"We will have more mines coming on stream with battery-electric vehicle technology almost monthly now as we go through the years," he said, noting that Sandvik's battery-powered electric vehicles are currently going online in their fourth Canadian mine.
Epiroc, another major electric mining equipment manufacturer out of Sweden, has 16 vehicles operating in Canada and expects to have 28 more online by the year's end.
Two recent Sudbury, Ont., mining projects have gone the route of full electrification, and other mines in Saskatchewan, British Columbia and Quebec are in various stages of implementing electric equipment.
Ali Madiseh, an assistant professor at the University of British Columbia's NBK Mining Institute and Canada Chair in mine energy systems, said the mining industry is looking for ways to reduce emissions, just like many other industries. For him, electric equipment is necessary to achieve that goal.
"With the technologies that we have at our disposal right now, electrification is the only solution," Madiseh said.
Madiseh notes that equipment only accounts for a portion of the industry's overall emissions output, so companies also have to decarbonize the power they generate if they truly want to reduce their footprint.
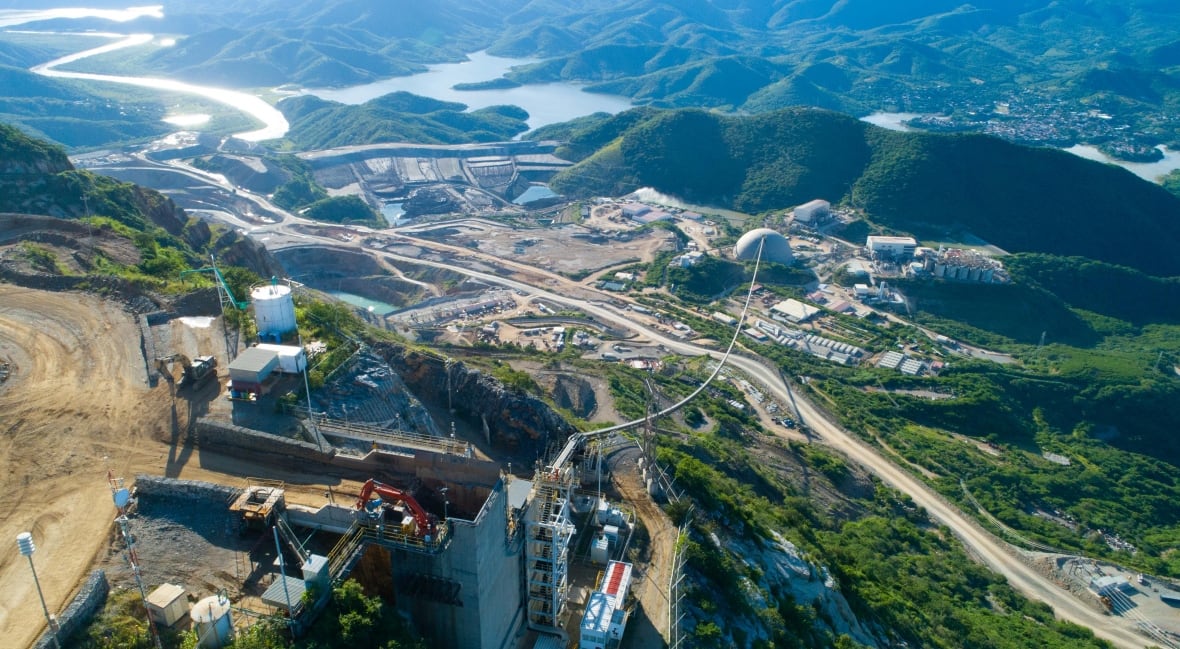
Financial benefits, health benefits
Torex, a Canadian gold mining company that operates in Mexico, says the future of mining is electric.
The company uses a fully electric rope-based conveyor system to perform work that would usually be done by diesel trucks, said Angie Robson, Torex's senior vice president of human resources, environmental, social and governance, and communications at Torex Gold.
Torex is also constructing a solar energy plant to help power their operations, a move Robson said will reduce their overall emissions by nine per cent per year.
The company found that using electric equipment also makes financial sense, especially in the long-term.
"We really were looking at this with the future in mind and the cost benefit did come out beneficial toward the EVs," said Robson. "But I think they'll actually prove even more beneficial as things evolve."
LISTEN | Are new regulations on diesel exhaust in Ontario's mines tough enough?
Most mines use complex ventilation systems — that can cost anywhere from $20 million to $400 million to install, and often require millions more per year to maintain — to regulate diesel emissions levels underground, said UBC's Madiseh.
By contrast, electric equipment doesn't produce fumes, which means companies don't have to spend as much on expensive ventilation.
"Diesel particulate matter — DPMs — are a huge concern, and the main reason you have ventilation in a mine is to dilute the diesel emissions," Madiseh said.
For Rakochy, the difference in air quality between mines that use diesel equipment and those that have electrified is stark.
"This will be a bit crude, but you generally will get up and you'll blow your nose. When you blow your nose, your Kleenex will be full of black soot," Rakochy said.
"You know that stuff has definitely gone into your nose and into your lungs. With battery-electric vehicle equipment, there's absolutely zero of that."
Particulate matter from diesel engine exhaust is carcinogenic and long-term exposure to these fumes lead to an increased risk of lung cancer and possibly bladder cancer. A 2018 study found that 2.4 per cent of cases of lung cancer in Canada are attributable to occupational diesel engine exhaust exposure, and underground mine workers were among the occupations with the highest risk.
This is one of the reasons why Unifor's Santos welcomes the change.
"From a worker standpoint we're happy with the move away from diesel, especially when you talk about some issues we've seen with diesel particulates," Santos said.
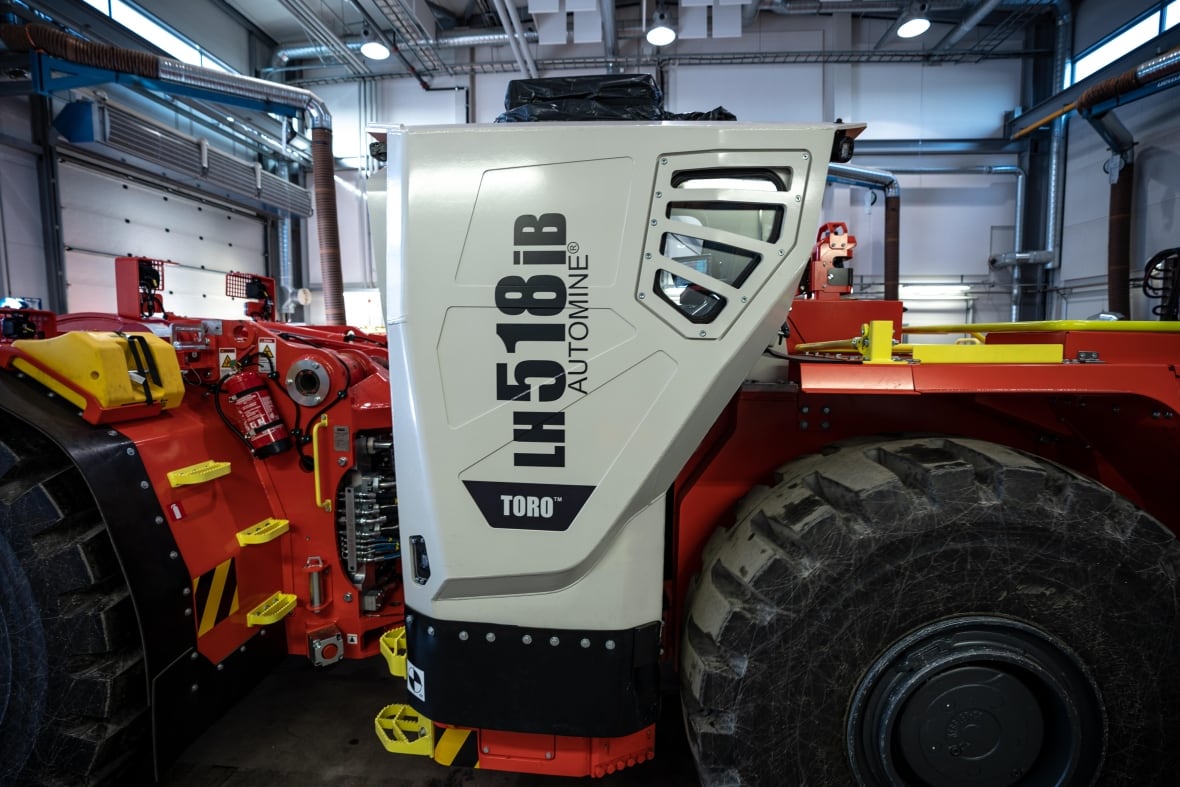
Safety concerns
But Santos says part of the challenge is that risks — like electrical fires and vehicle collision hazards — differ between worksites. It can be difficult to spot these risks until the equipment is operating on location, he said.
Given the confined nature of mines, Santos says his main concern is battery fires, a worry shared by Tom Welton, the director of health and safety services and education programs at Workplace Safety North.
"It's not seen very often. If it does happen it can result in catastrophic effects," Welton said.
Welton's risk assessments found that fires usually resulted from damages to the battery itself, or through improper handling.
WATCH | This company upcycles old diesel trucks:
Sandvik's Rakochy agrees that fire is a risk with battery-powered mining equipment, but he says this is also the case with diesel equipment. He says mitigating this risk is a matter of proper education and management.
Workplace Safety North identified collisions as the most common risk associated with battery-electric vehicles, which are considerably quieter than those with diesel combustion engines. While that means less strain on the hearing of workers, it also means there's an increased risk of mining vehicles going undetected.
"Battery-electric vehicles can be very quiet and can move very quickly throughout a mining operation and potentially put pedestrians in hazard's way," Welton said.
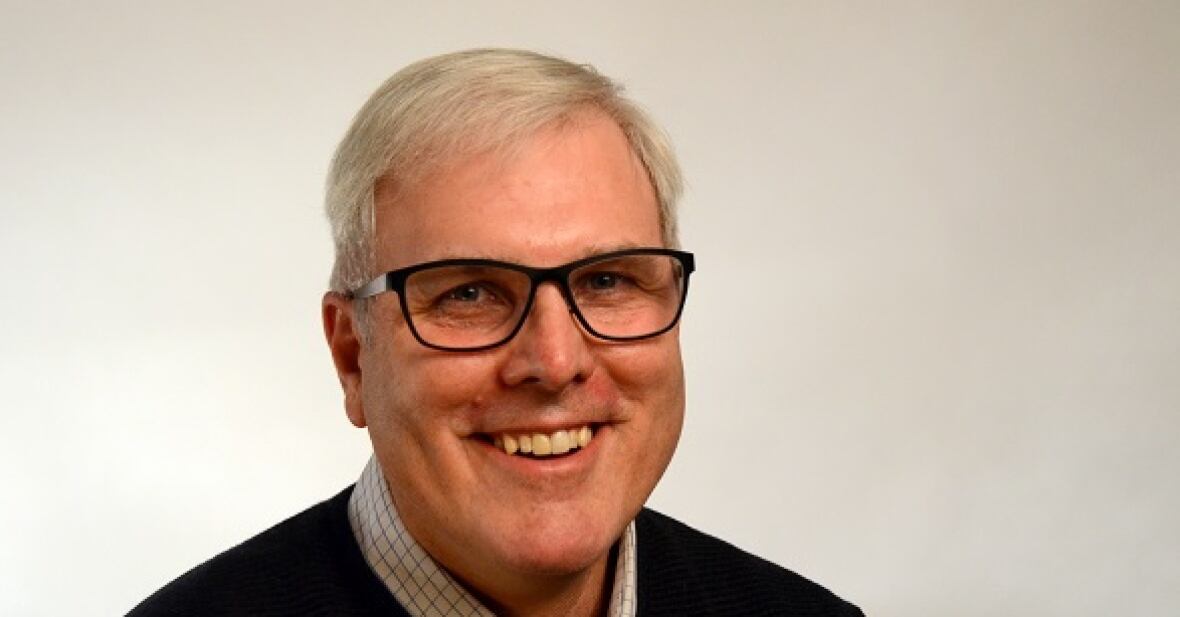
Last year, new workplace standards for electric mining vehicles were introduced. Welton says he's glad the standards introduced voltage range limits for underground mining equipment, and provided measures for the operation and maintenance of electric equipment, but says more protocols are needed.
For instance, he notes there are no regulatory requirements in place for charging stations — one potential source of battery fires. Likewise, while Welton notes that manufacturers have been supportive in providing training to the workers using this equipment, he also says training is a "weakness" in the industry.
Cambrian College and Collège Boréal in Sudbury have both started offering industrial battery-electric vehicle maintenance training programs within the last two years. Welton is working with Ontario's Mining Legislative Review Committee to identify areas of need and establish new safety standards for the industry.
"There's different challenges and hazards, especially with the voltage that you're dealing with," Welton said. "It has to be dealt with appropriately."